The below animation depicts an axisymmetric model of a mono-tube gas shock absorber, with its schematic beside it. The piston inside the casing pushes its way through the oil (the hydraulic fluid which in reality is a mixture of oil and gas) creating resistance as the oil is pushed through the small holes in the piston. The contact between the piston (solid model) and the casing is modeled by specifying a friction coefficient, which is usually very small due to the lubrication provided by the oil.
The spring is initially extended and then released. Its subsequent motion is damped by the oil flowing through the holes in the piston. The figure below shows the acceleration of the piston during a 0.2-second damping event.
The results for the simulation were obtained using the TR-BDF method (trapezoidal rule / backward-differentiation formula), a composite one-step integration method that will be available in ADINA 8.1 for both fluid and FSI analysis. It is second order accurate and L-stable. Therefore, spurious oscillations that may appear when using the trapezoidal rule are not present. Furthermore, high accuracy is still achieved. Another advantage of the TR-BDF algorithm over the trapezoidal rule is the accurate calculation of the accelerations in the solid model.
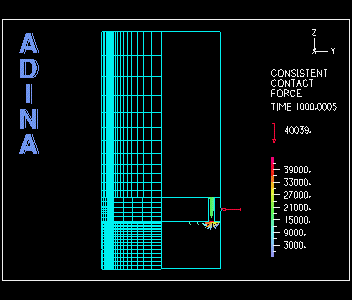
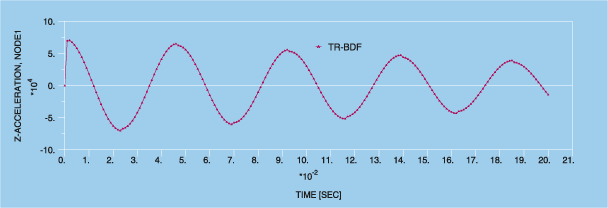