MWH GLOBAL / TYSELEY RESOURCE RECOVERY CENTRE
BIRMINGHAM, UNITED KINGDOM
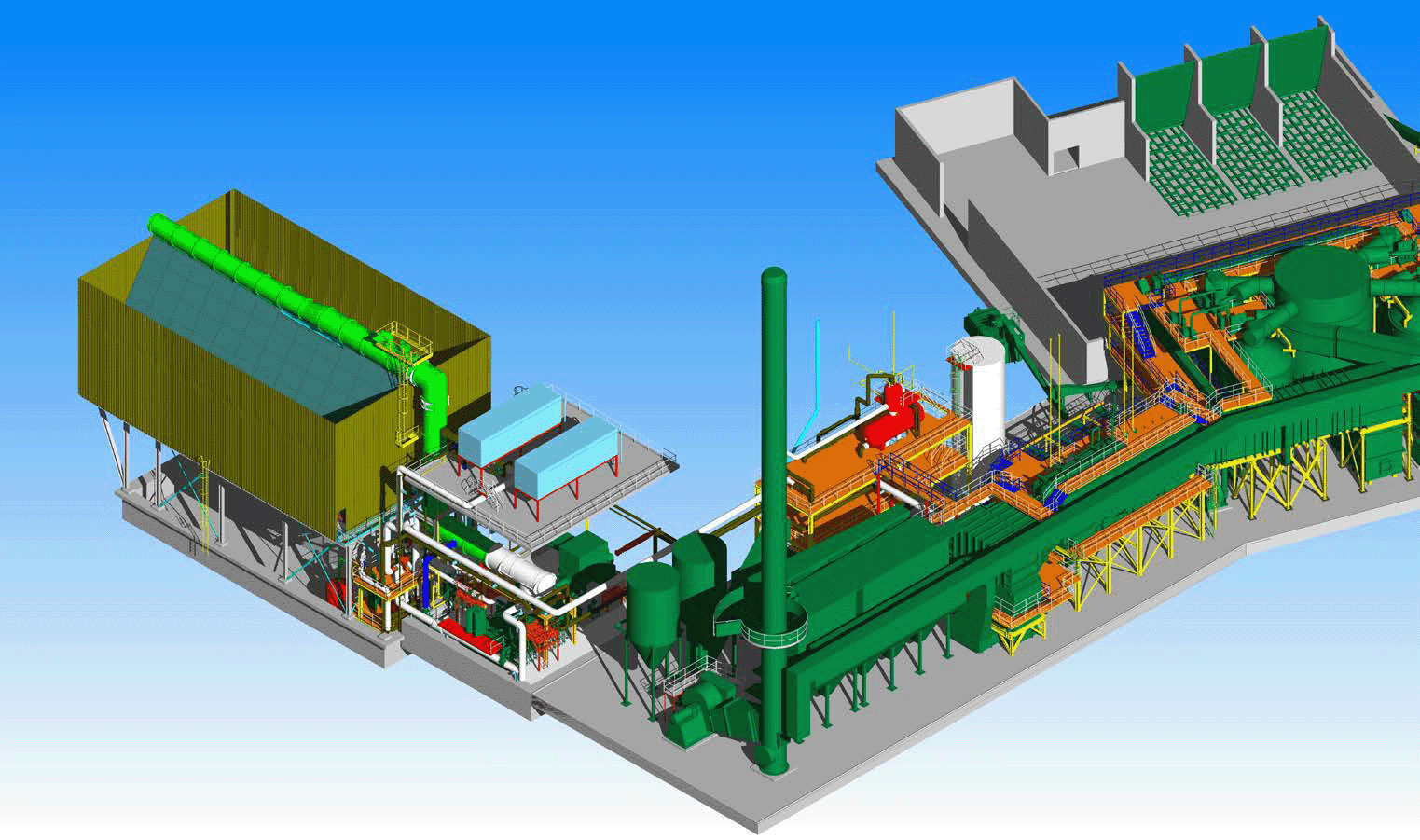
Project
Generating power through the gasification of 67,000 tons of waste wood per year, the GBP 48 million Tyseley Resource Recovery Centre will be the first of its kind in the United Kingdom. Over its 20-year lifespan, the plant is expected to supply enough electricity to the national grid to reduce greenhouse emissions by 2.1 million tons, divert 1.3 million tons of waste wood otherwise destined for landfills, and generate enough renewable energy to supply power to 17,000 homes. The owner, Birmingham Bio Power, selected MWH Global as the EPC contractor for this high-visibility project.
Facts
- Project delivery costs were reduced through flexible import/export of various formats and applications, and automated report generation, quantity take-offs, and isometric generation.
- Use of intelligent 3D models helped reduce costs by enabling virtual project progress meetings, facilitating virtual walk-throughs, and mitigating risk in problematic or hazardous areas.
- The team improved the safety of the project by using 3D models in access, lift, and maintenance reviews to identify and mitigate safety issues.
“Bentleyās OpenPlant applications truly helped in our project design delivery and enabled us to stand tall in the crowd.”
– Ashish Katake, Lead CAD Designer, MWH Global
Solution
Working with multiple suppliers and subcontractors, MWH needed a 3D design environment that enabled end-to-end collaboration. The advanced functionalities of Bentley software allowed MWH to create intelligent 3D models for use in design reviews, clash detection, and virtual walk-throughs, as well as to produce deliverables required for construction and operation. Bentley applications helped the team to efficiently collaborate with suppliers to avoid rework, and to conform to project delivery standards.
Outcome
OpenPlant PID produced intelligent process and instrumentation diagrams which facilitated importing and exporting of P&ID i-models to sync with mechanical piping models, and exporting of pipes for pipe stress analysis. Other efficiencies such as model collaboration, design data synchronization, and deliverables production saved significant time and costs in project delivery. After construction and commissioning, MWH will take on an operational role running the plant under a five-year operations and maintenance contract.
Software
OpenPlant
MWH selectedĀ OpenBuilding Designer,Ā MicroStation, and OpenPlant to develop and coordinate the design for Birmingham Bio Power, and enable efficient mobility of information across various stages of the project.
ProjectWise
The team usedĀ ProjectWiseĀ to share design data and information across disciplines and among various MWH offices in the United Kingdom and India, allowing MWH to optimize a common methodology, design delivery workflow, and engineering standards.